PRODUCT OVERVIEW

With the rapid development of the society economy, the traditional ultrafine powder processingequipment can no longer meet the market demand and requirements in the ultrafine powderprocess field due to the low capacity. In this background, having accumulated multiple yearsexperience in manufacturing mills, Clirik has designed and launched a new-type CLUM seriesvertical roller mill on the basis of introducing the vertical roller mill technology from Taiwan andGermany,which integrates the functions of grinding,classifying, conveying, secondaryclassifying, and packing progress into one machine. lts powder fineness can reach 400-3000mesh. The CLUM mill breaks through the bottleneck of low capacity mentioned herein. Over 5years’development, more than 30 ultrafine powder production lines have been installedworldwide.
APPLICATION FIELDS
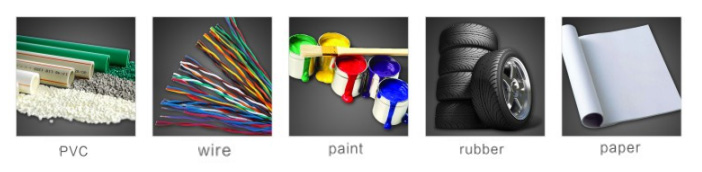
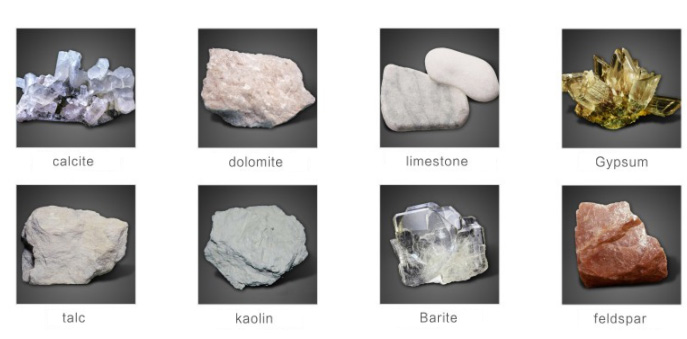
CLUM series ultrafine vertical roller mill can be widely applied in the industries of chemicals.metallurgy, non-metallic ores etc. In particular, it is outstanding in processing white superfinenon-metallic ore powders, providing superior quality fillers and additives for paper makingcoating materials, plastics, rubber, PVC, printing ink etc. The CLUM mill can be extensivelyused to process superfine dry powder of non-mental materials such as calcite, marble,limestone, dolomite, barite, talc, kaolin, wollastonite, gypsum,feldspar, pyrophyllite etc.
MAIN STRUCTURES

CLUM series ultrafine vertical roller mill mainly consists of the motor, reduction gear, grindingrollers, grinding plate, pressure-applying device, classifier, mill body, oil station, and electricalsystem.
Grinding roller: Main component for crushing and grinding materials. No power input when the grinding
plate turn rotary, the rollers are rotated passively by friction force after touch the materials.
Grinding Plate: The area for grinding process, to be rotated and driven by reduction gear.
Pressure-applying device: Control the grinding roller and plate gap, keep the roller pressure.
Classifier: Multi-rotor classifier, utilize the rotated centrifugal force to separate the fine powder during thecontinuous process. lt is a highly-efficient and energy-saving powder separating device.
WORKING PRINGIPLE
Grinding process
The grinding plate is rotated by the main motor via the reduction gear. Meanwhile, highpressure air enters the mill interior via the air inlet. Materials then fall onto the center of thegrinding plate in rotation by the screw conveyor feeder. Due to the centrifugal force, thematerials evenly move from the center of the grinding plate towards its fringe. While passingacross the track in the grinding plate, large blocks of materials are crushed and grinded directlyby the grinding roller. The fine particles form the material bed, owing to squeezing, where theinter-particle crushing takes place until grind to the fine powder.The fine powder continue to move towards the fringe of the grinding plate until they are takenaway by strong air flow at the air ring. While the materials along with the air flow pass throughthe separator located above the grinding plate, the coarse particles return to the grinding platefor re-pulverization due to the action of the rotor blade, the fine particles along with the air flowleave the mill interior and are collected and discharged as finished powder product by thepowder collector.
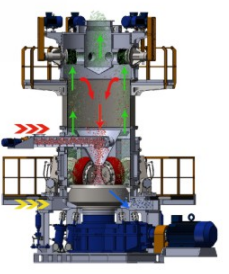
Final product quality guarantee
The coarse granular and impurities will fall into the lower grinding chamber, and be discharged
out by the scraping plate.
High-precision multi-rotor classifier adopts frequency control, adjustable rotor speed,
produces various particle size.
Adjusting the hydraulic system pressure to change the roller pressure, fit for materials with
different hardness.
Electronic caging device makes sure the safety gap between roller and plate, effectively avoide
the heavy vibration due to lack feeding.
TECHNICALADVANTAGE
Use the special anti-wear alloy materials forgrinding roller and plate liner. Long service time for wearparts, low maintenance. The grinding curves of the rollershell and liner plate are uniquely designed, easy to form thestable material bed, low vibration, high product efficient. ltis 20% higher than other equivalent vertical mill in capacity,saving 40% power consumption compared with ball mill.